SAFETY CONTROL SYSTEM (TECHNOLOGICAL)
The USBT digital technological safety control system for NPP units is designed to initiate actuation and control safety systems.
Functions of USBT:
- monitoring technological parameters and identifying initial events by primary processing of input signals and generation of current signals in three mutually redundant MSKU channels;
- generating sequence of protective action commands by “2/4” logic that are stipulated for a detected initial event (protections of emergency core cooling system, pressurizer’s pulse valves protections, shut-down cooling protections, step-by-step diesel generator starting algorithms, etc.);
- generating technological protection and interlock commands by “2oo3”, “2oo2”, “1oo2”, “1oo1” logic (protections and interlocks of steam pipe and feeding pipe systems, main steam isolation valve, a technical water system, gas blowers, ventilation systems and conditioning, oil pumps, etc.);
- automatically regulating technological parameters;
- automatically controlling actuators;
- remotely controlling and indicating actuator state in MCR, BCR;
- generating technological and warning alarm signals in MCR, BCR;
- transferring data on technological parameter values, state of protections, interlocks, and actuators, diagnostic data to unit’s IVS;
- visualizing, archiving, and logging current data.
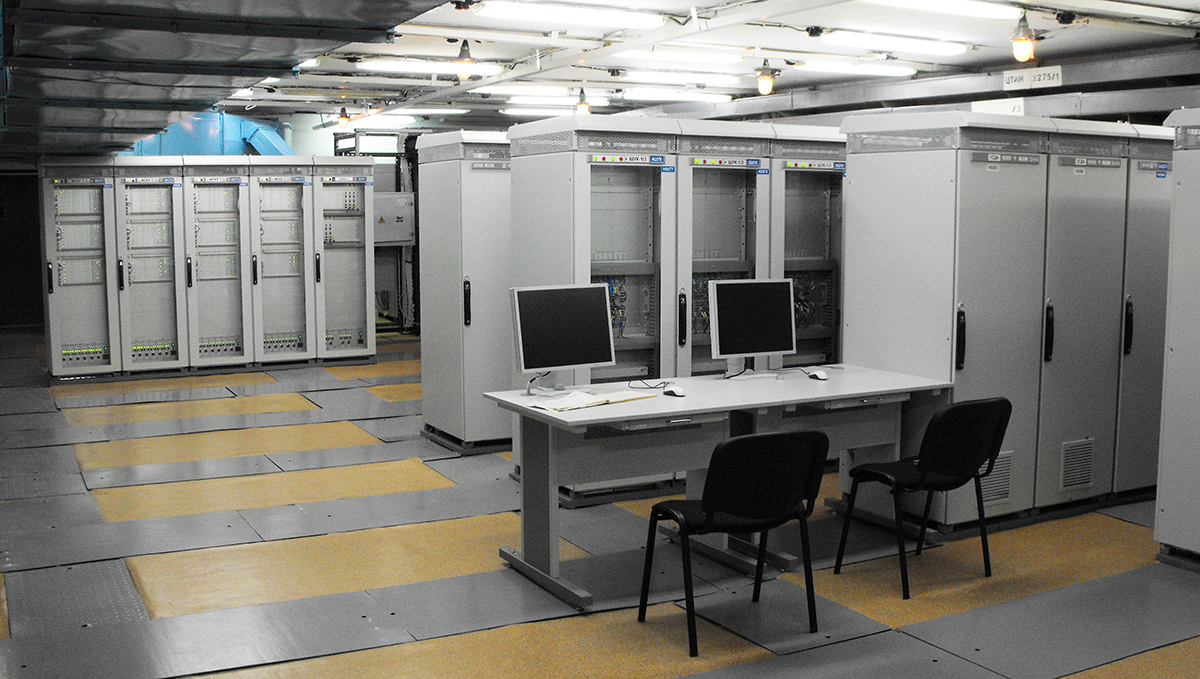
Composition of USBT:
- a subsystem of control and measurement instrumentation and current signal distributors – implements primary processing of input signals with assurance of redundant power supply of primary converters, generates current signals for external users (implemented based on industrial controllers of MSKU series);
- a control and switching subsystem – implements generation of sequence of protective action commands, commands of technological protections, interlocks, and alarm, as well as arrangement of internal information exchanges between USBT components via digital fiber-optical communication lines (implemented based on ShUK cabinets);
- an automatic regulating subsystem – assures generation of control actions for keeping technological parameters (pressure in steam generators, primary circuit cooling speed, level in steam generators in emergency modes, etc.) in accordance with specified regulating algorithms, monitoring of analog signal input channel operability, and realization of specified control algorithms in case of failures (includes MSKU SAR implemented based on an MSKU industrial controller and an IS SAR engineering station implemented based on a PS5140 workstation). A SAR subsystem (automatic regulating subsystem) with equipment for communication with an operator’s panel may be supplied separately as a SAR USB system;
- a subsystem of actuator control – generates signals of control and state of lock, air-operated isolation, regulating valves’ actuators, discrete output signals to adjacent subsystems (is implemented based on ShDS and ShKr cabinets);
- a subsystem for communication with an operator – assures implementation of functions of remote control of actuators, indication of actuator state, technological alarm and warning alarm (implemented based on devices for communication with an operator’s panel (USPO remote controllers in MCR) and alarm panels with a project based set of alarm annunciators);
- a technical diagnostics and archiving subsystem – assures reception, processing, visualization, archiving, and logging of data on state of technological parameters, actuators and data of technical diagnostics of USBT, adjustment of online changeable parameters, and transfer of current data to an upper level network of unit’s IVS (includes diagnostic and archiving servers implemented based on a PS5140 industrial workstation).
System advantages:
- high tolerance to failures due to use of redundant hardware (MSKU three-channeled industrial controllers, redundant USPO, ShDS, ShUK cabinets and workstations);
- ergonomic and intuitively clear operator’s interface;
- high level of system’s security to cyber threats;
- convenience of operation and maintenance due to a modular structure of system’s components with the possibility of fast swapping of faulty modules.
Safety class – 2.
Safety category – А.
Implementation facilities:
- Zaporizhzhya NPP, units 1-5
- Khmelnitsky NPP, unit 2 (in the scope of SAR USB)