MPC-U MICROPROCESSOR BASED INTERLOCKING SYSTEM
MPC-U – a microprocessor based interlocking system carrying out all functions of monitoring and safe control of train movement at stations and spans.
It implements route and individual control of field equipment of any kind, remote control of shunting zones and yards, coupling with the upper level’s systems.
Functions of MAB-U and MPAB-U are integrated into MPC-U. To monitor vacancy of track sections, track circuits or axle counting systems can be used.
Structural principles of MPC-U allow to implement the following:
- division of large sections to control zones (both permanent and seasonal);
- selection of sectors with the function of temporary local control at a station with shunting operation;
- remote control of adjacent stations and track towers.
It can be used to construct MPC of stations with the following parameters:
- number of switches up to……………256 pcs.;
- number of signals up to……….........256 pcs.;
- number of track circuits up to….......512 pcs.
|
|
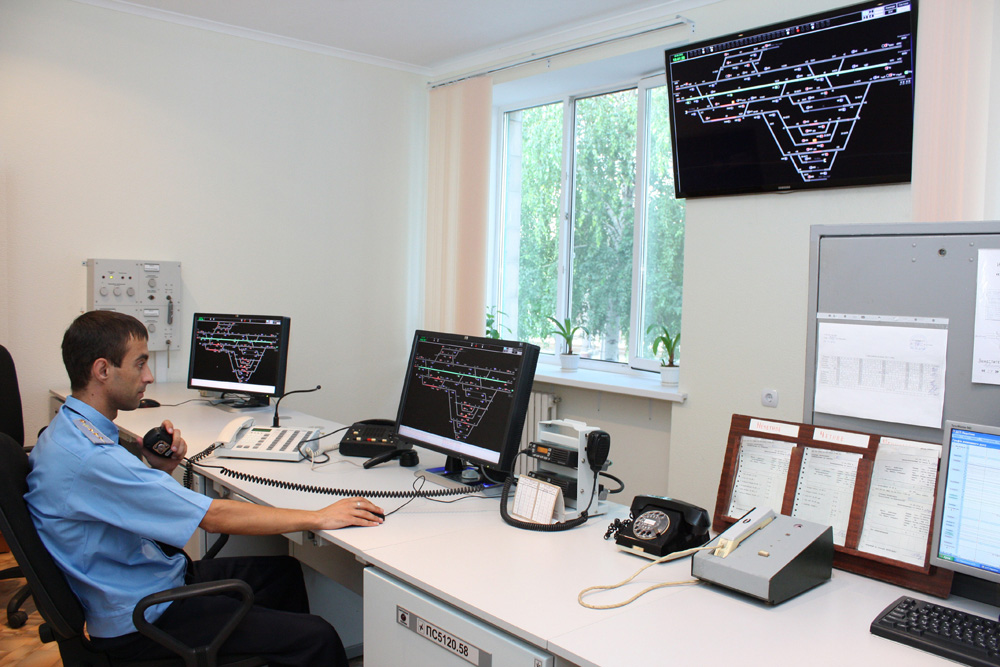 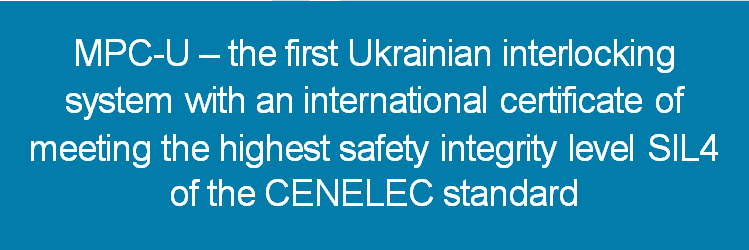
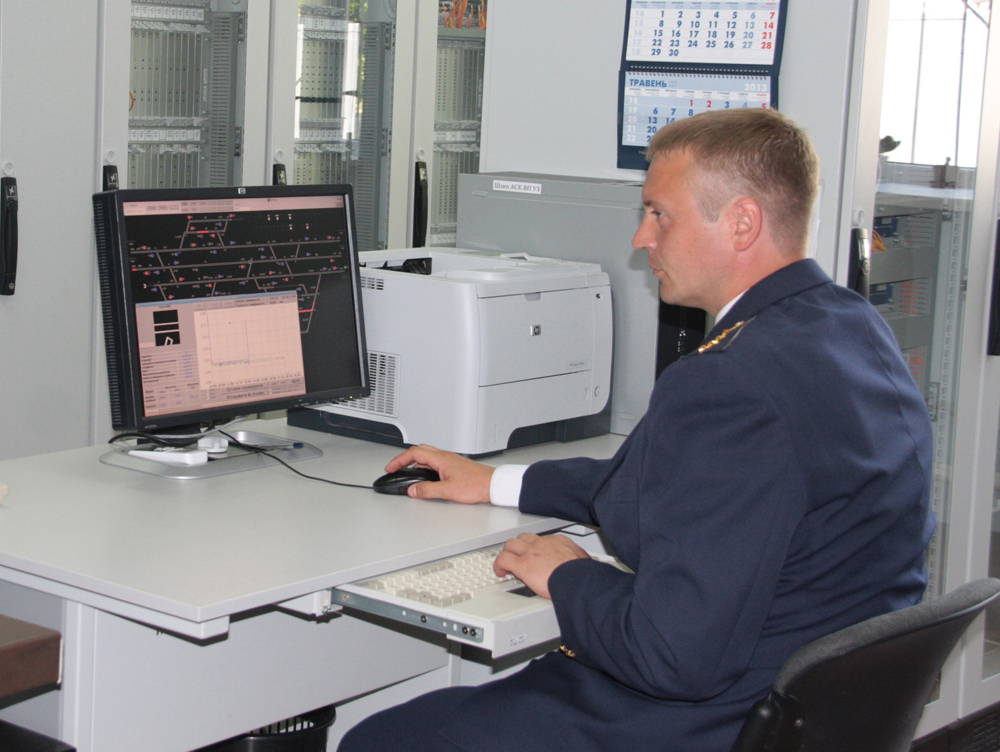 |
Main functions of MPC-U
- monitoring and control of processes of train reception, departure, passing, overtaking, shunting operation at a station;
- train movement safety assurance on routes:
- setting, release, and cancel of routes;
- control of traffic light signals;
- coding of train routes with signals of automatic locomotive signalling (ALS);
- automatic unlocking of shunting routes during angle runs;
- switching on of a call-on signal;
- individual switching and automatic return of tongues;
- artificial release of sections;
- switching off of switches and isolated sections with preservation of use of signals;
- setting of a route without opening of a signal;
- coupling with level crossing, pedestrian, tunnel signalling with individual time lag for each signal being opened;
- individual counting of time lag for each route cancelled and section released;
- display of reliable information concerning a train position and a state of signalling devices at ARM of an assistant station master (DSP) and ARM of a technician (ShN);
- monitoring of a power supply system;
- logging of actions of operating and maintenance personnel, archiving of all information received, and forming of logs and reports required;
- check of awareness of operator actions when setting important control commands.
|
|
 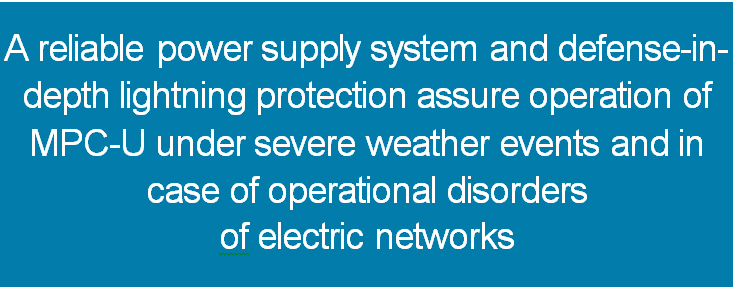
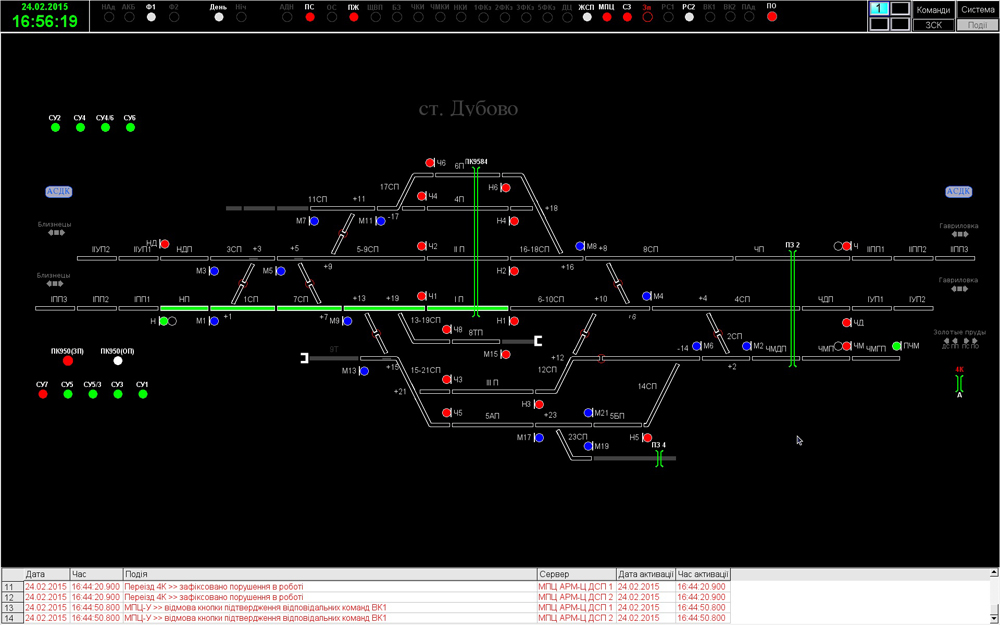 Video frame of ARM DSP |
Structure of MPC-U
The modular structure of the hardware and the software assures use of MPC-U at large, medium, and small stations. The systems differ only in number of object controllers required to connect the signalling devices and configuration of the application software. The equipment of MPC-U can be located both in a centralized and in a decentralized manner.
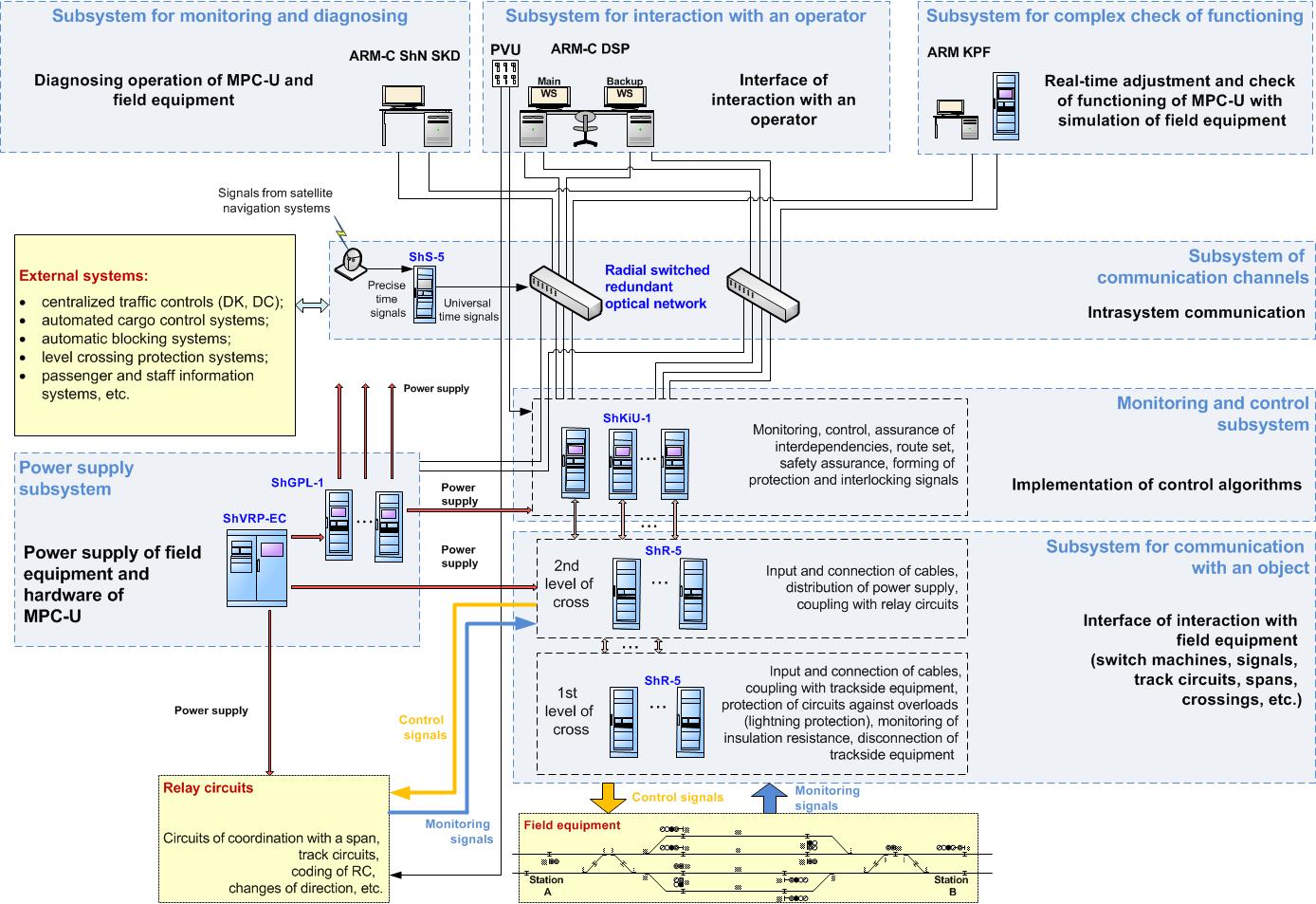
Functional scheme of MPC-U
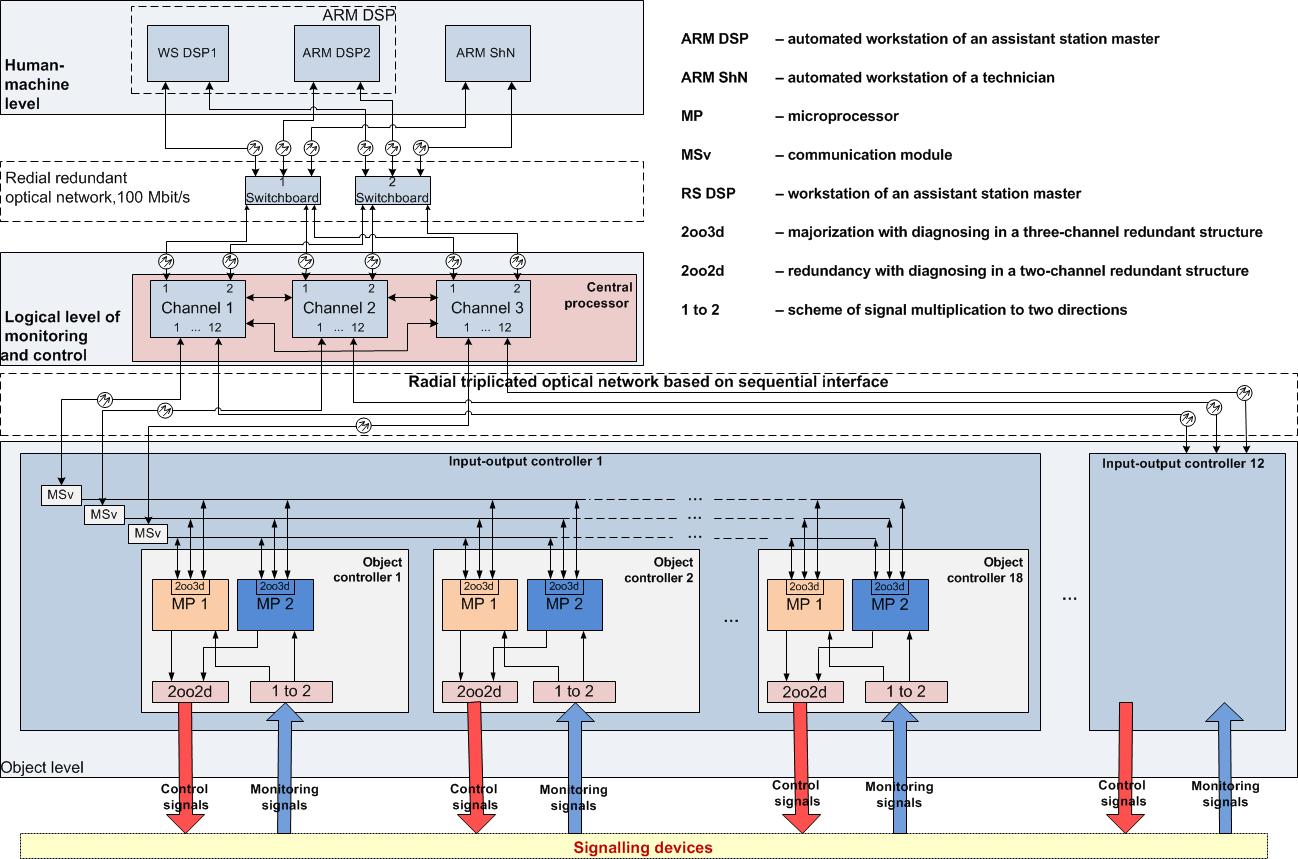
Structure of MPC-U
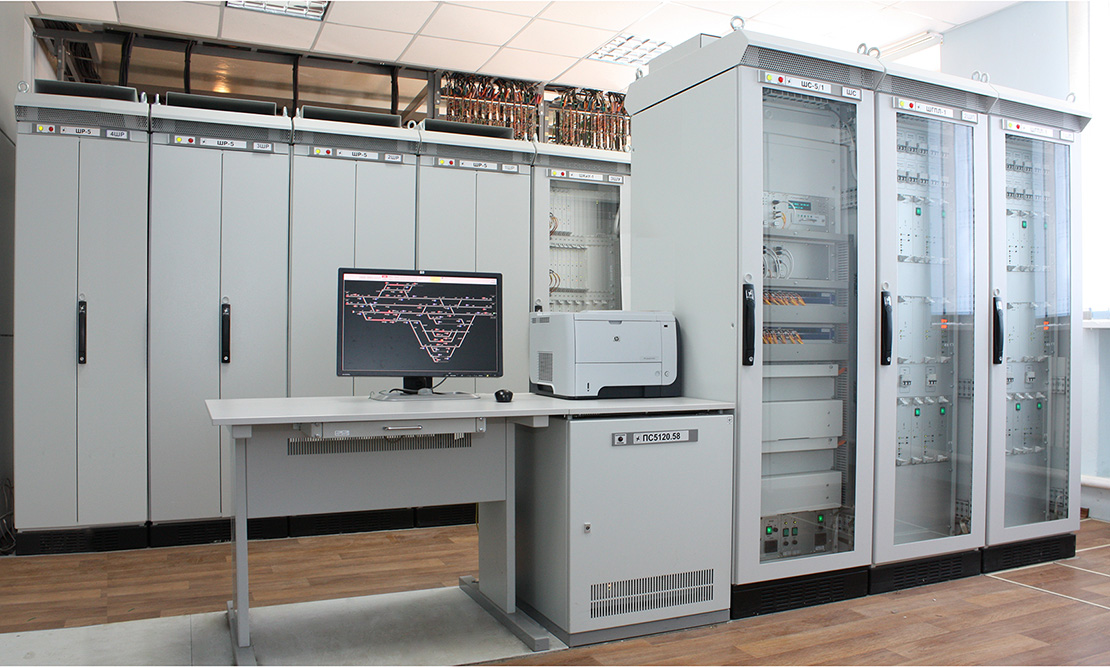
MPC-U at a station (relay room)
The main solutions to assure functional safety and reliability of MPC-U include as follows:
- the three-channel structure of the safe central processor working by the “2oo3d” scheme (voting with diagnosing) with diversification of the software. If one of the channels fails, operation continues by the “2oo2d” scheme (redundancy with diagnosing), and information on an error is recorded in the database. A faulty module can be replaced and put into operation without stopping the system;
- internal redundancy of object controllers, each having two diverse channels and operating by the “2oo2d” scheme, and control commands from three channels of the central processor are processed by the “2oo3d” scheme with reconfiguration if one of the channels fails (2оо3d → 2оо2d);
- single defects of the hardware and the software don’t cause dangerous failures and are detected by operating and testing impacts;
- connection with the help of a redundant fibre-optic cable by the “dot-dot” scheme between each channel of the central processor and each input-output controller (failure of any connection doesn’t influence operation of other connections);
- redundant version of ARM DSP, possibility to add additional ARMs DSP;
- security of interaction of an operator and MPC-U:
- impossibility to create a situation dangerous for train movement by incorrect operator’s actions during operation in the main control mode;
- clear indication of operator’s actions, as well as check of consciousness of his actions in the auxiliary control mode (repeated request to an operator and reception from him of a corresponding answer confirmed by pressing of a special button);
- strategy of safe behavior in case of failures (failure resistance);
- continuous monitoring and diagnosing of states of the signalling devices and the MPC-U software and hardware with data acquisition, processing, storing, and display at ARM ShN.
|
|
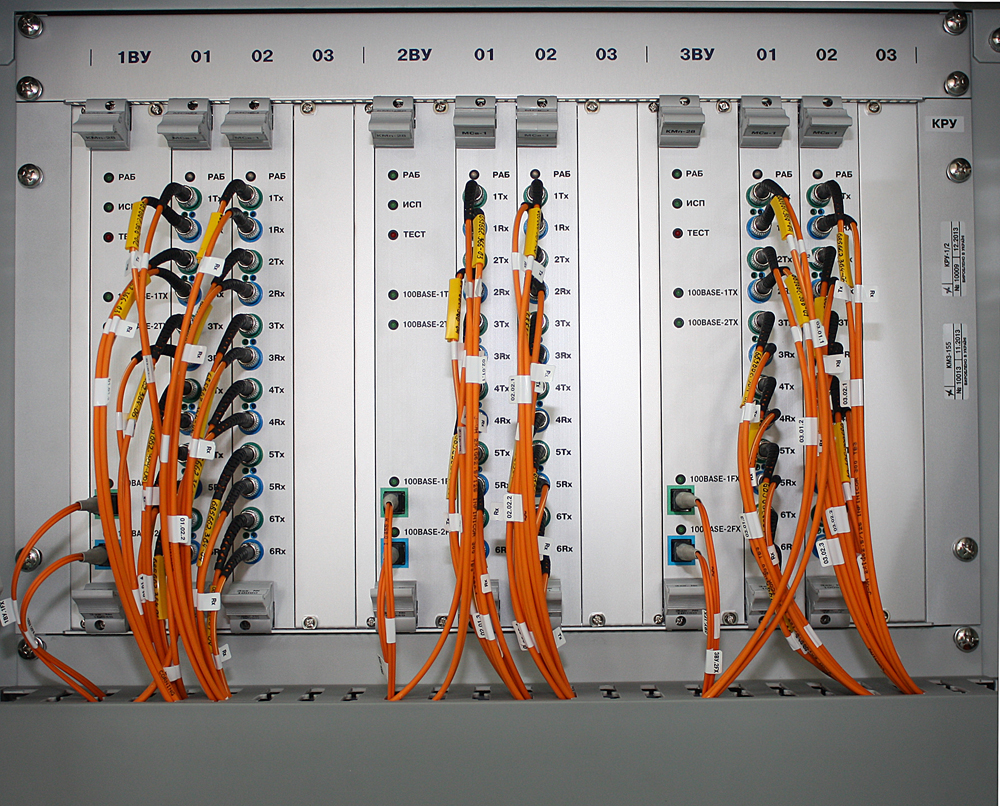 Safe central processor 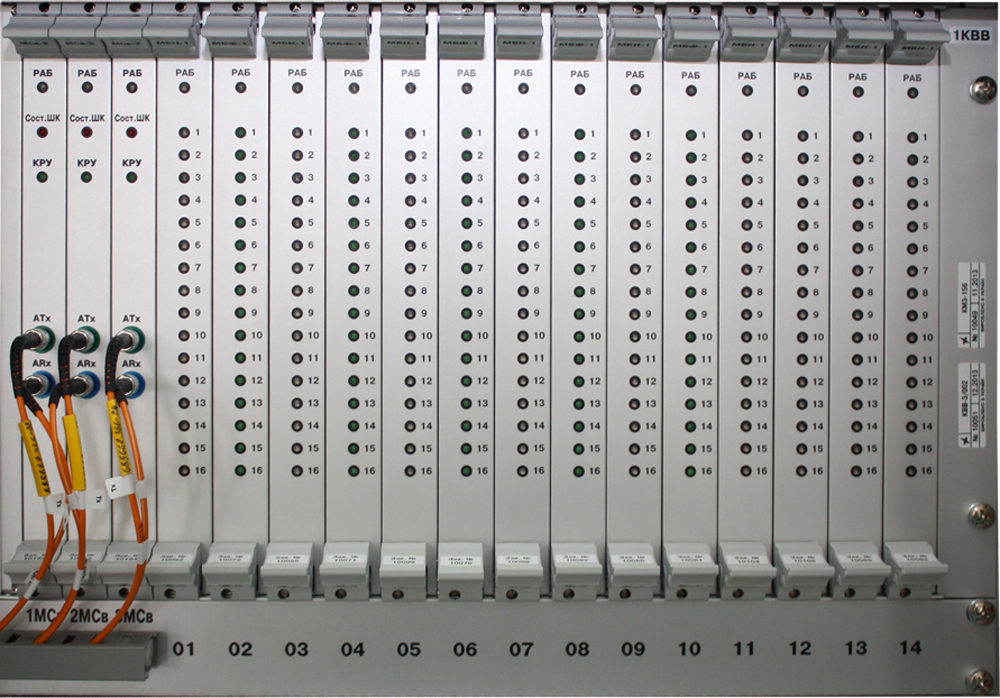 Object controllers |
System advantages
- high safety level meeting both European (CENELEC, SIL4) and national safety standards;
- possibility to construct interlocking systems in accordance with the standards of the “area 1520” and the European standards assuring safety of operation (ERTMS/ETCS);
- cyber security of MPC-U meeting the requirements of the corresponding ISO and IEC standards;
- contactless control of switches and signals eliminating relay components completely;
- the software and the hardware approved in MPC-U are the basis to construct other systems (MAB-U, MDC-U, MRC-U, etc.), assuring high characteristics of unification, reliability, and safety of signalling;
- availability of all required interfaces for coupling with different electric interlockings (EC), centralized traffic controls (DC), traffic control systems, etc.;
- use of the computer-aided design system when developing and modifying the application software with protection against unauthorized access;
- availability of the common-timing system receiving exact time signals from satellite navigation systems;
- reliable protection against atmospheric and switching overvoltages, short circuits, pulse overvoltages;
- absence of fans (as the most unreliable elements) to remove heat from electronic components;
- a version of the MPC-U equipment allowing placing it in transportable modules and operating in a wide range of climatic conditions.
|
|
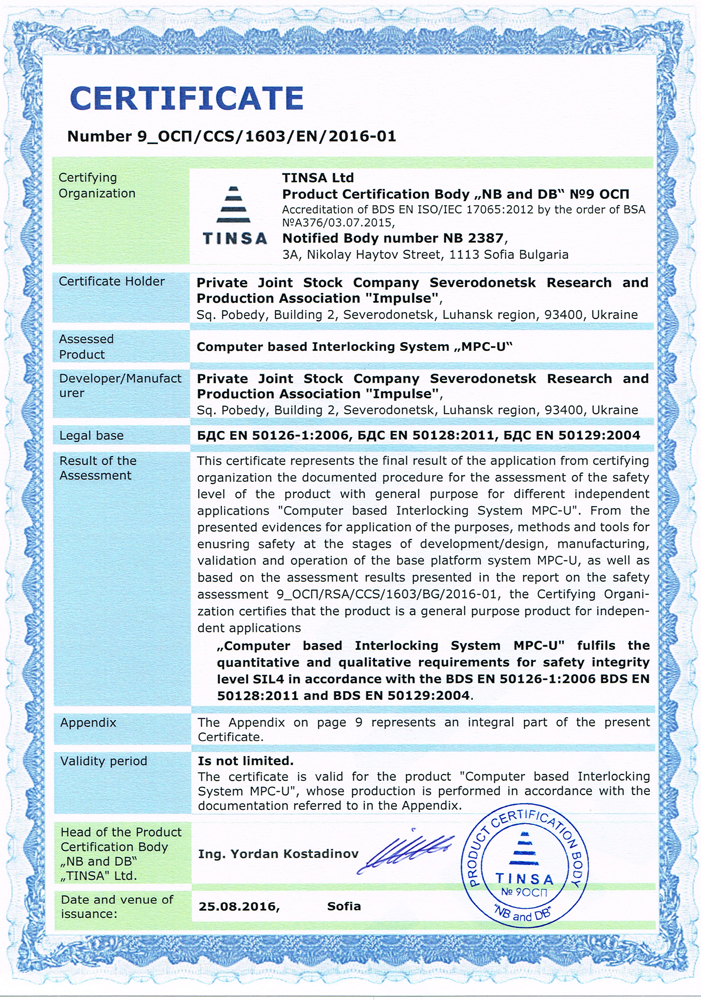
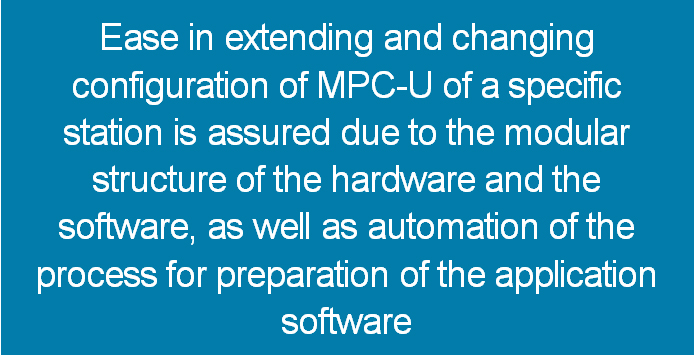
|

|
|
|
Fire safety requirements
1. MPC-U meets fire safety requirements according to SOU 45.020-00034045-002, GOST 12.1.004, NAPB А.01.001.
2. MPC-U is not an ignition source, does not propagate and does not sustain fire. Fire risk of the MPC-U hardware does not exceed 1•10-6 per year according to GOST 12.1.004.
3. Nonmetallic structures within the MPC-U hardware are manufactured of low-combustible nontoxic materials, without hazardous substances capable of effecting life and health of servicing staff.
4. Ignition sources do not occur in used purchased articles during current overloads, short circuits, or failures. When being delivered all required certificates for meeting fire safety requirements are provided.
5. Used cables do not propagate fire according to DSTU 4809 and have required supporting documents.